Situation
Garfoot Project Services was asked to provide project management and site management services on behalf of a manufacturing company. The project involved the replacement of cooling towers with a higher capacity and modernised cooling solution.
Challenge
The existing cooling water plant utilised two cooling towers which were ageing and would be unable to cope with planned capacity increases for the site. The client had specified a desire to lower the risks of legionella and reduce the need to use toxic chemical treatment such as chlorine.
The project would need to deliver a new cooling system, capable of handling the increased demand whilst fitting in the same footprint as the old cooling towers. The system would need to integrate into existing cooling water pipework and not be reliant on chemical treatment.
Additional challenges included:
- Space was congested, airflow to the area restricted.
- Efficiency would be a driving factor, opting for ambient cooling rather than refrigeration circuits.
- Existing pipework and valve design was outdated.
Additional challenges included:
- GPSL was brought in after completion of the design phase, however the URS had not yet been finalised.
- The site was production critical, meaning downtime of the system was extremely tight.
- Existing control systems were not fully understood or documented making integration difficult
Solution
Working with company specialising in industrial cooling systems, a design was selected which used an ambient air cooler fitted with a set of sprays to provide an adiabatic cooling effect on hot days.
The new system would feature of these units. To address the issue of airflow, the units would be mounted on a gantry and use a V-Block design to draw air in from the sides, unobstructed by other plant. The sprays would use water with an automatic drain-down function to ensure water was not stored in pipework and therefore negating the need to control legionella through chemical treatment.
The old cooling towers would be disconnected and extracted by crane, before lifting the new gantries and coolers into position. The system was re-piped using existing control valves, allowing for minimal disruption to site services.
Results
The cooling system was effective. The spray system was tried out very shortly after install due to the time of year and the client was pleased to see that critical process temperatures were maintained within safe operating limits.
Connecting to the existing system proved to be more complicated than previously expected due to limited design information available from the original installation, however this was overcome by a thorough survey of the pipework by the supplier to generate new P&IDs which assisted in the new installation.
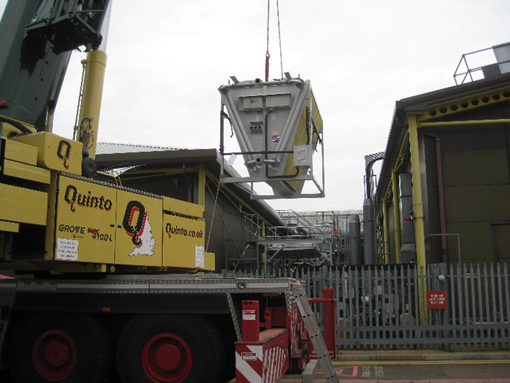
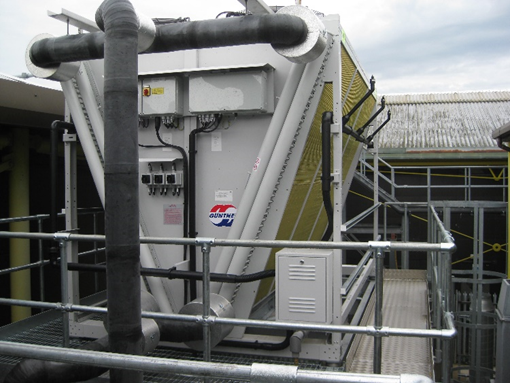