Situation
GPSL were awarded an 18 month contract to provide project management and validation support on behalf of a medical device manufacturer for the upgrade and capacity expansion of a manufacturing process.
Challenge
The client was looking to expand the production capacity of a process supporting the development of medical devices. The expansion would require three additional process rigs to meet capacity demands. The processing plant uses large volumes of highly flammable solvent maintained at high temperatures and the bulk of the processing plant (vessels, pipework etc) is made of industrial glass. As part of the works, the project would need to provide an upgraded PLC control system to replace the existing out of date control cabinets.
Additional Challenges:
- Production to the site would need to have minimal interruption.
- COVID-19 protocols (social distancing, testing, hygiene) would be in place for installation, commissioning and validation.
- To minimise personnel numbers, GPSL would take on the site management role on behalf of the principal contractor to ensure compliance to CDM regulations.
- Operating in and around plant containing extremely hazardous chemicals.
- HAZOP and LOPA reviews required for the new plant.
- Compliance to GMP validation procedures.
Solution
A competent process systems company, specialising in glassware process systems for hazardous chemicals, would be appointed as principal contractor. Additional contractors would include an automation integrator, electrical systems supplier, and mechanical engineering supplier.
GPSL, liaising with the client to verify requirements and seek approval, would develop a suitable URS for the new system and work with the various suppliers to deliver the solution. The three additional processing rigs would be installed and integrated into the existing process systems. New ATEX Zone 2 electrical cabinets and cabling would be installed for the new rigs. Existing control system hardware would be upgraded with new PLCs and integrated with the new control system installed for the expansion.
Once installed, the system would need to be full validated using GMP V-Model methodology
Results
Initial project timelines had been set prior to the pandemic but were re-baselined following a review of the working procedures to enable compliance with social distancing. The project fully delivered the clients requirements.
This high value project was delivered on time and on budget. There were no reportable safety incidents and no lost day cases due to covid.
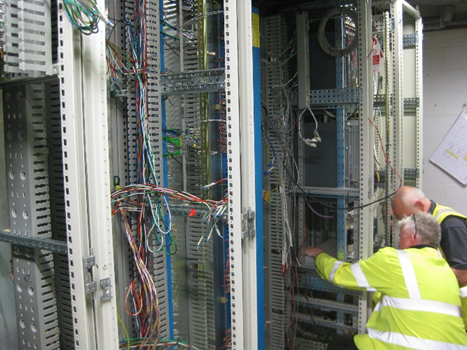
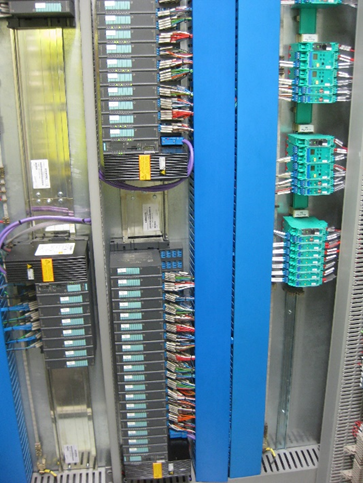