Situation
Garfoot Project Services were awarded an 18 month contract to project manage the relocation of injection moulding machines (IMMs) and assembly equipment used for the manufacture of baby feeding bottles and accessories.
Challenge
The client was looking to expand the production capacity of its baby soother products. To enable this expansion, four hydraulic IMMs used to manufacture components for baby bottle sterilisers, and machinery used to assemble breast pumps needed to be relocated from one building to another building on the same site and re-validated in accordance with GMP.
As part of the works, new power supplies, compressed air supplies and IT networks would need to be provided.
Additional Challenges:
- Supply of product was critical, machine downtime could not impact the supply chain to customers.
- Compliance to GMP validation procedures
- During the project, the customer’s company made announced the closure of the manufacturing site with all processes transferred to overseas sites.
- The original planned moves would continue through to full validation.
- Mass redundancies on site, high level of sensitivity and discretion required.
- Following completion of relocation and validation sign off, GPSL’s scope was expanded to include managing the transfer of the same equipment to multiple overseas companies in Europe and Asia.
Solution
GPSL would develop a detailed project definition document and plan. Internal maintenance/engineering resources would be utilised to prepare the equipment for relocation, and external contractors used to provide the necessary additional services (power, air and IT networks). A specialist machine moving company would be brought in for the relocation of the IMMs whilst internal resources could be used for relocation of the assembly equipment.
Following relocation of the IMMs and the assembly lines, full validation would be completed and a PUWER assessment arranged to enable production to resume.
To carry out the transfer of IMMs and assembly equipment following the site closure announcement, GPSL would provide project management support for the transfer of this equipment and for other additional machinery on site.
GPSL would participate in the selection process for the manufacturing sites that would receive the various equipment. This includes providing benchmark data of the existing equipment, full supporting documents and reviewing the equipment status/condition with potential new owners of the equipment. GPSL would coordinate the decommissioning and dismantling of machines ready for shipping overseas, and manage the packing and shipping of the equipment by the specialist machine movers, ensuring compliance with international shipping regulations.
Results
Initial project timelines for the relocation and re-validation of the IMMs and assembly equipment was completed on time and on budget. Teamwork and professionalism of those impacted by the site closure was critical to achieving the project goals.
Following the internal relocation of the equipment, production was quickly back up to full output levels.
The decision to close the site had a huge impact on those employed full time with all employees being made redundant at various stages of the closure. During this phase GPSL were sympathetic to those affected whilst we completed the machine moves from the UK site to the new sites in Europe and Asia.
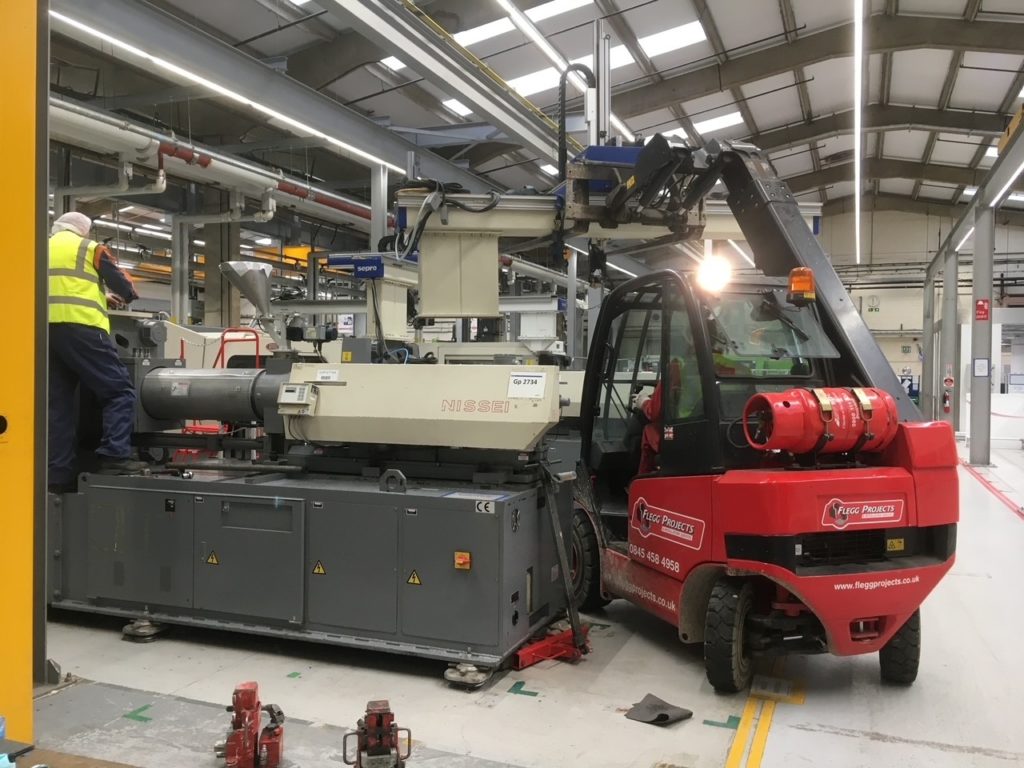
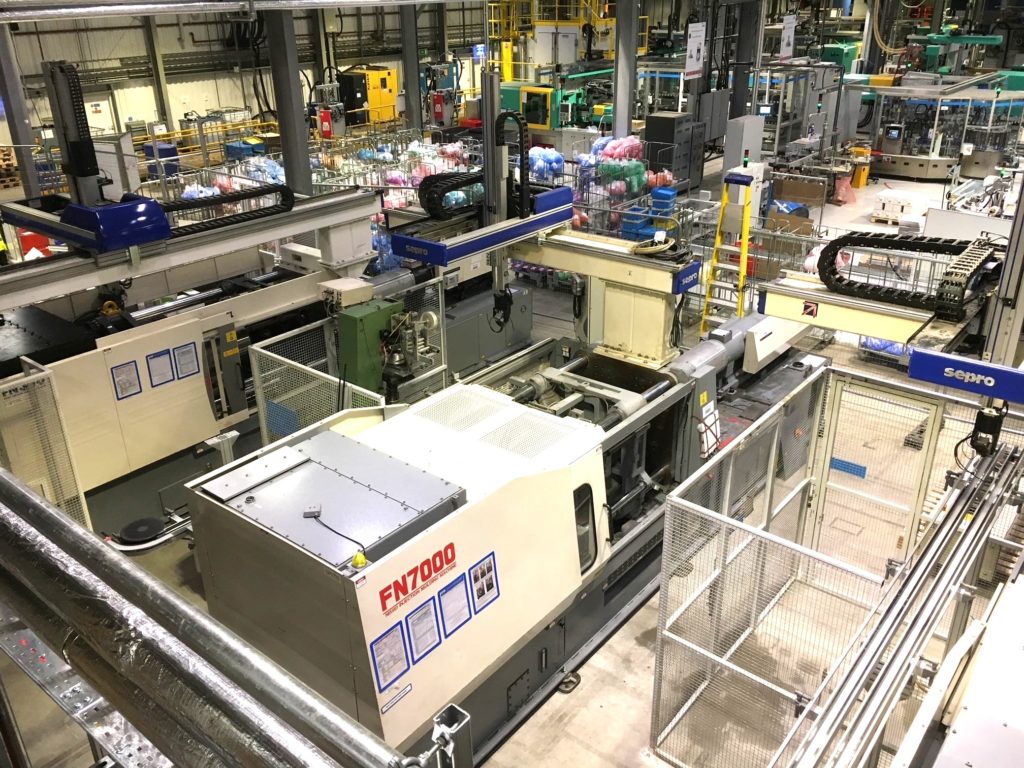